A Review of Fuel Tanks as well as Their Development Over Time
- Maggie
- Aug 27, 2020
- 2 min read
The approach of control of a liquid within a storage tank has actually not altered enormously since the dawn of the chemical, pharmaceutical and also oil and also gas processing sectors. A particular process calls for claim one or several sorts of liquid to work as maybe an additive or a coolant as well as these fluids require to be securely consisted of however also easily given as well as renewed.

At a fundamental level this receptacle could be the matching of vat of beer or a skid steer loader fuel tank or even a milk bottle - relying on the procedure relies on the simpleness or the elegance of the fluid supply vessel. Safe containment of these liquids is necessary because their leakage can affect significantly upon the setting as well as cleaning up after a spill is really expensive. The style of, as an example, a fuel tank is regulated by a variety of technological and visual factors to consider which likewise can have an influence upon the tools's design and expense. The product originally used for a fuel tank was steel which is conveniently developed and also can be securely bonded effortlessly. Its kind was typically square or rectangular so it could be quickly dealt with as well as likewise contain an easy float kind degree sending device. The common drawback of steel storage tanks was their capacity to rust if not appropriately secured and this was a well-known trouble. As the development of moulding plastics advanced it emerged that plastic fuel containers used a number of advantages over their steel alternates. The rotomoulding process of making a tank includes injecting a known quantity of plastic granules into a warmed revolving mould tool in the form of the container.
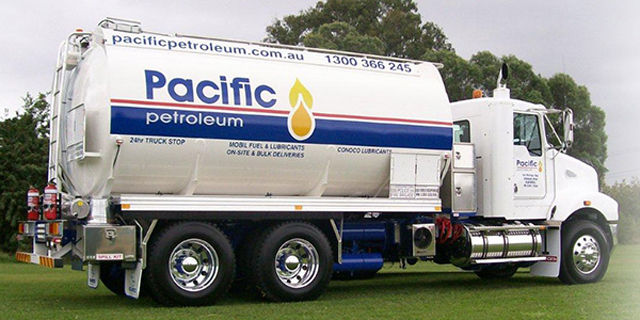
When the device is disintegrated after cooling you have a container of elaborate style which can be pierced for pipework entry or installations for a drain plug or level sender etc. This indicates the form of the storage tank can suit the contemporary designing accounts located today on building tools which is what the client is requiring. Sensing unit modern technology has actually not developed extremely considerably throughout the years yet the method of packaging the sensor element has actually done so mostly due to ever more demanding operating and ecological factors to consider. As an example, modern race as well as rally autos work at much higher temperatures as well as pressures than in the past which develops ever before increasing layout challenges for sensor makers. This in turn filters to port as well as circuitry makers that have to stay up to date with the requirements established by the button maker.
Comments